
Commercial Pad Printing
ABOUT the pad printing PROCESS
Pad Printing as we know it today is one of the newer printing technologies. It was born from the need to commercialize printing on uniquely or specialty shaped items and supported by the mass production of silicone for industrial use. Unlike traditional printing processes, pad printing allows designers and engineers to place text and imagery on virtually any surface - from flat to spherical and concave to convex. Pad printing can even achieve accurate results on textured (uneven) surfaces - something no other printing process is able to achieve.
“Pad printing
can design
textured or concave
surfaces.”

Sample Pad Printing Container Design Projects
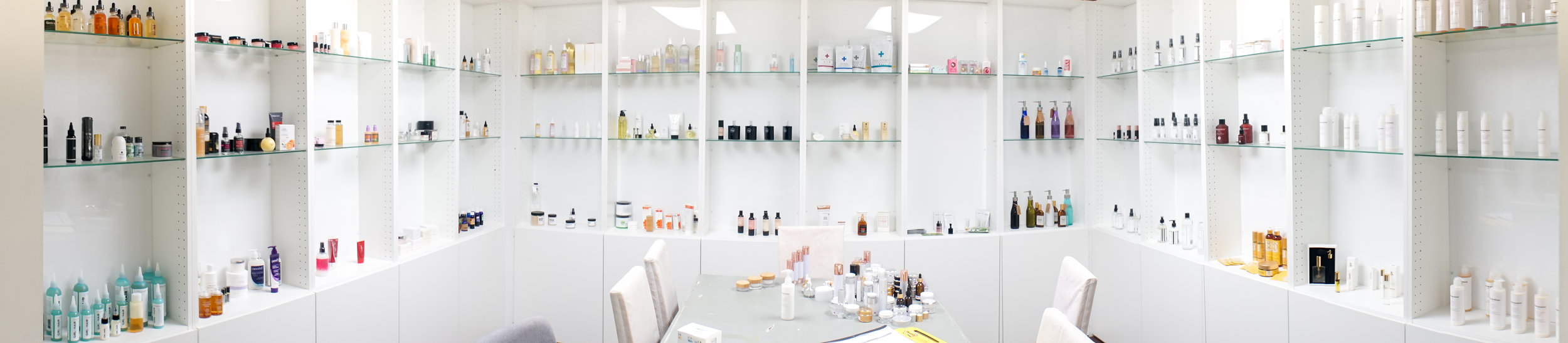
How
The Pad Printing Process
The container or closure design is etched onto a plate made of photopolymer or a specialized polymer. For each color used in the design, a new plate is created. These plates are loaded onto a pad printing machine corresponding to the ink color. As each container passes through the machine, each design plate is filled with the ink. The silicone pad is stamped onto the ink and transferred over to the final product (called the substrate in the industry). The silicone pad’s ability to mold to the final printed surface is what makes this method perfectly suited for specialty shaped containers.
Color
Pad Printing with Multiple Colors
We can print with a large selection of colored inks, from standard colors to custom PMS (Pantone Matching System) colors to create an exact match to your branding. There is a multitude of ink finishes to choose from including high-gloss, metallic, opaque, and satin, as well as specialty inks for added flexibility and durability. There are pad printing processes specially formulated for nonstandard surfaces such as wood, polypropylene, ceramic, metal and glass.
Brand
Branding with Pad Printing
The Pad Printing method can be used to add a logo, imagery, or text to glass, plastic, metal or even paper. The final products can range from promotional giveaways (such as custom golf balls, vinyl balls, translucent plastics, and ice packs) to industrial parts. The ability to add multiple colors to a single design makes it easy to recreate your branding on anything. With the ability to transfer inks to a 3D surface, you also get a seamless look that creates a lasting and durable mark.
Glass
Pad Printing on Specialty Glass Bottles & Jars
Uniquely shaped glass containers are used in a number of industries for both aesthetic and practical reasons. For example, in the liquor market, alcohol brands are conceiving new glass bottle shapes to increase brand visibility and improve product quality/shelf life. For this industry and many more, pad printing offers individualized solutions to help companies capture their brand identity with sophisticated container designs that compliments its uniquely shaped container.
Metal
Pad Printing on Specialty Plastic & Metal Containers
Pharmaceutical, industrial and mechanical industries are often at the cutting edge of product and packaging design innovation. New products are continually entering the market with irregular designs specific to their purpose: formed metal parts, injection molded plastics, and medical devices, just to name a few. Pad printing allows for these new (and generally uniquely shaped) products to be branded and marked. Aside from branding, units of measurement and simple instructions can be clearly illustrated with pad printing
Trend
Pad Printing Trend - Organic Appeal
As the demand for organic and naturally derived products rises, brands are shifting to a “label-less” look. Pad printing is the perfect solution for a minimalist look process that supports the organic, green or sustainability-related aspects of the product.
Versus
Pad Printing vs Screen Printing
When should you choose pad printing versus screen printing? Screen printing is advantageous for larger sized designs, while pad printing should be limited to printing on a targeted area. There are varying setup costs associated with each as well, regarding the creation of silk screens and pad printing plates. Every job is unique, with many factors to consider associated with the type and use of the final product, so it’s best to make the decision under the guidance of an experienced printer.